CNC Spinning Machine Processing Data Input
Date: Apr,11 2020 View:
CNC Spinning Machine Processing Data Input
The input of processing data in the CNC system of the CNC spinning machine is an important link. The core part of the system CPU has a first-level capacity and computing capabilities, with the ability to input, calculate and edit processing data, as well as the ability to judge, calibrate and correct the signals sent by external sensors.
The data input methods of CNC spinning machine are roughly as follows:
(1) Digitizer method. First, draw the outline of the workpiece on the drawing and the secondary line (track line) of the roller path on the drawing board, and the drawing can be drawn according to the scale. Then move the digitizing converter along the drawn curve, and the roller path is converted into data in the form of a set of X-Z coordinate values, and recorded with a cassette tape or disk. Except for the secondary line of the roller, other forming conditions, such as the thickness of the blank and the wall thickness of the workpiece, the shape of the roller, the feed speed and the spindle speed, etc., are written into the part program according to the language format used and input with the keyboard. Then transfer the input data to the display screen of the computer and edit it according to the forming process. At this stage, if necessary, you can enter auxiliary forming processes such as workpiece trimming and beading. Then use the information processor to sort the entire format again. Convert it to NC data and record it on an information carrier such as a magnetic disk, so that it can be transferred to a spinning machine for operation.
The position reading accuracy of digitizer is generally ± 0.1 ~ ± 0.25mm
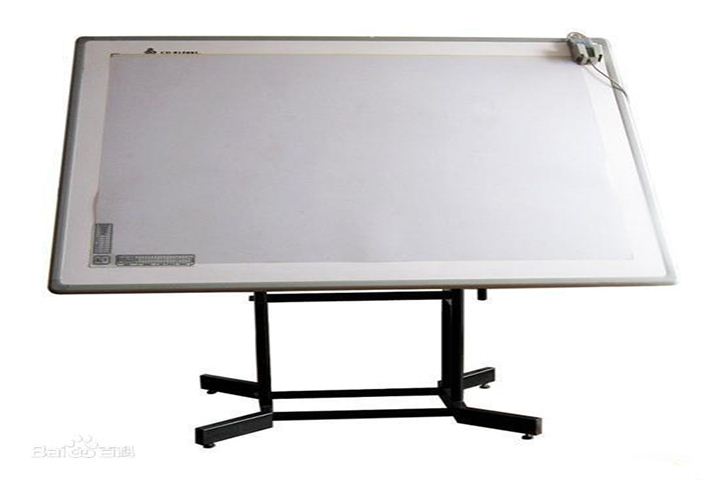
(2) Curve template (bar) method. The above input method using the digitizer method has a slight disadvantage in the input speed and data accuracy. Therefore, an input method using a curve mode can be used. The so-called curve template refers to inputting the microcomputer from the existing forming experience data, selecting a group of pass shapes with the highest frequency of use, and then performing three algebraic approximations respectively to obtain the best mathematical model and inputting it into the microcomputer as the control model. This method can shorten the data input time, and can simultaneously control more than two rotary wheels, so that the mutual position of the two remains highly accurate.
(3) Use the offline computer or directly use the microcomputer to modify the CAD / CAM drawing programming on the spinning machine's console, and use the disk to record storage and input. The picture shows a CAD drawing design drawing of a workpiece spinning. This chart is used as the basis of programming-the main program can consider other data after it is determined (such as the subroutine of spinning machine performance, raw materials, tool geometric parameters, the angle of the tool holder and the size of the drawing). After inputting the starting point, the processing form can be gradually input to the microcomputer in the programming language. At this time, geometric data or analog-to-digital converters must be used to collect and add control points on the trajectory of the roller. In addition, auxiliary forming such as trimming and curling is added to the parent program as a subprogram.