Metal Spinning Technology Improving Product Surface Quality
Date: Oct,20 2020 View:
Metal Spinning Technology—Improving Product Surface Quality
(1) The indentation of roller on the surface of spinning part is related to the roller fillet radius and the feed speed of roller. A large roller fillet radius and a small feed speed generally make the surface smooth.
(2) The working surface of the roller is best to be ground and polished
(3) In order to make the inner surface of the product bright and beautiful, the surface of the core mold should be plated with wear-resistant chromium and polished.
(4) The different viscosity coefficients of the lubricating oil used will have different effects on the surface quality of the product. The surface with a large viscosity coefficient will be uniformly darkened, and the surface with a small viscosity coefficient will not be uniform. For materials such as aluminum, since a lot of peeling powder will be produced during spinning, it is better to use a lubricant with a low viscosity to wash it away.
(5) When spinning aluminum and copper materials, it is best to gently push with a cemented carbide indenter to get a good finishing effect.
(6) If vibration occurs when pressed with a cemented carbide indenter, a piece of urethane rubber can be clamped on the back of the indenter for cushioning.
(7) When spinning aluminum, the use of hard plastic rollers can achieve good results, and it is easier to grind and polish the rollers. However, during multi-pass deep drawing and spinning, some marks will be left on the surface of the product.
(8) When spinning hard materials, you can use cemented carbide rollers
(9) As shown in the figure, when the spinning is close to the end, the flange of the product meets the boss of the core mold, and the body of the finished product may produce small wavy protrusions, which will deteriorate the surface quality.
(10) If the wall of the product is too thin, it will produce back-extrusion as shown at A in the figure, resulting in irregular shape of the product
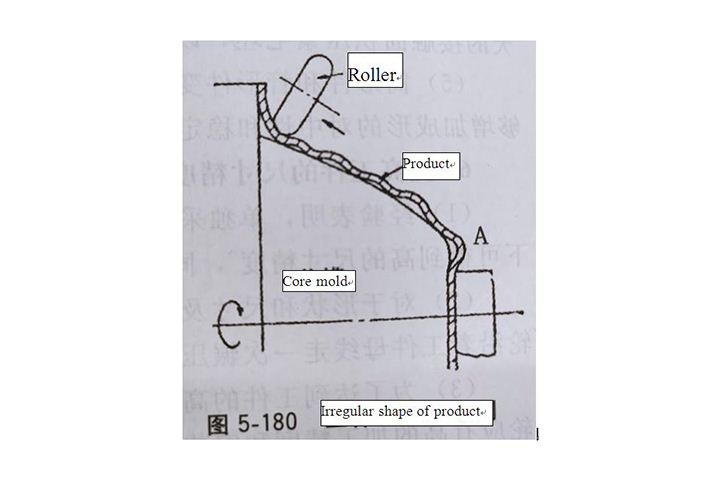
(11) The deflection of the rotating roller and the core mold during spinning due to manufacturing, processing or installation adjustment will affect the finishing quality of the product surface
(12) For aluminum or copper spinning, a hard plastic core mold can also be used, but it is not suitable for mass production because its wear resistance is not good.
(13) In order to eliminate the spinning traces of the roller, a flat roller can be used to flatten it.
(14) If vibration occurs during spinning, the surface of product will become rough. This is often because the gap between roller and core mold is selected too small, or there is a problem with the adjustment of the hydraulic profiling valve, which must be adjusted separately.
(15) In order to reduce the roughness of the inner surface of the workpiece, it is best not to lubricate the contact part of the workpiece and the core mold, so that the blank and the core mold are in direct contact to obtain finishing and forced polishing.
(16) In the case of conical parts or curved generatrix shaped parts with large diameter differences in spinning, the surface roughness is required to be uniform, and the spindle speed and the longitudinal feed speed of the spinning wheel must be steplessly adjusted, that is, the realization of the spinning process The feed rate of the rotating wheel remains unchanged, so that the surface roughness of the workpiece tends to be uniform and the surface quality is improved.